Materials
The materials your slurry tanker’s tank is made from are important but should also be viewed in combination with the overall design and construction. After all, there’s no point in having the best materials if they are poorly put together.
Nevada’s tanks are made from quality European S235JR steel, a non-alloy structural steel made in accordance with the EN 10025-2 standard. S235JR steel is widely used for machine building and is ideal for tanks as it is strong while being able to be rolled, welded, and hot-dip galvanised for protection.
For added strength Nevada tanks also include internal baffles and anti-implosion rings.
Design
A tank may look simple enough, but there is a lot of thought that goes into the design and functionality. A tank must be designed in a way that not only ensures structural integrity, but also to ensure long term durability – you want the tank to be strong and stay strong!
Nevada’s tanks are completely cylindrical, and effluent from the auto-filling arm is entered into the tank from the front centre of the tank for an unimpeded flow to the spreading applicator at the end of the tanker. This minimises any crevices effluent can become trapped in, and therefore corrode the inside of the tank, reducing strength.
A full chassis on models 10,000L or larger means the tank sits independent of the chassis to ensure movement impact is absorbed by the chassis and not transferred to the tank. While this doesn’t increase the strength of the tank itself, it does mean the tank is not having to handle any unnecessary additional pressure.
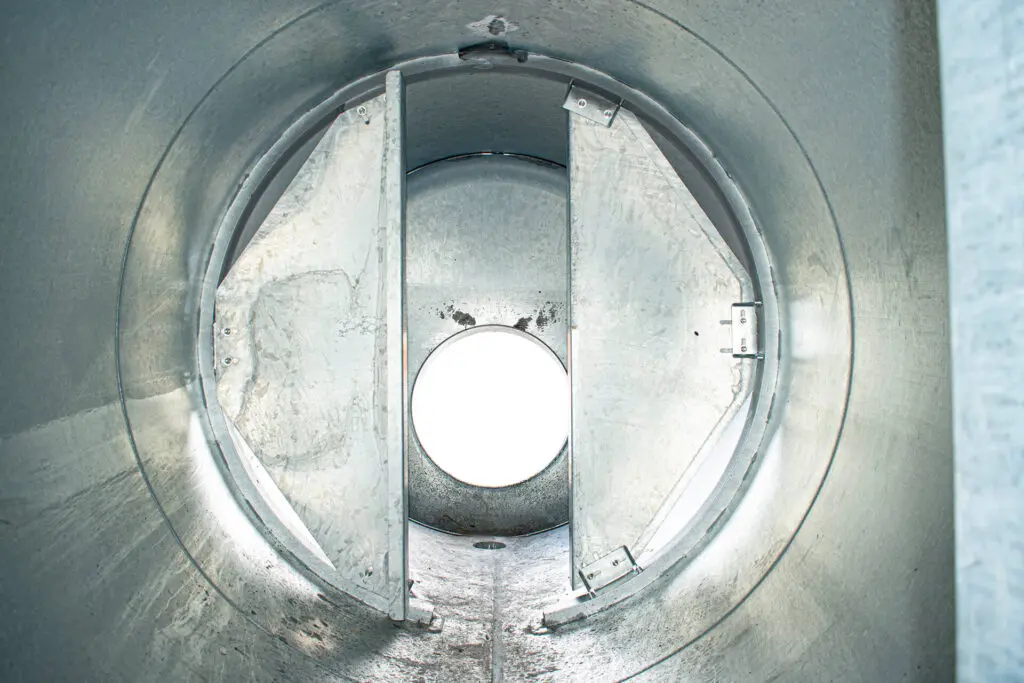
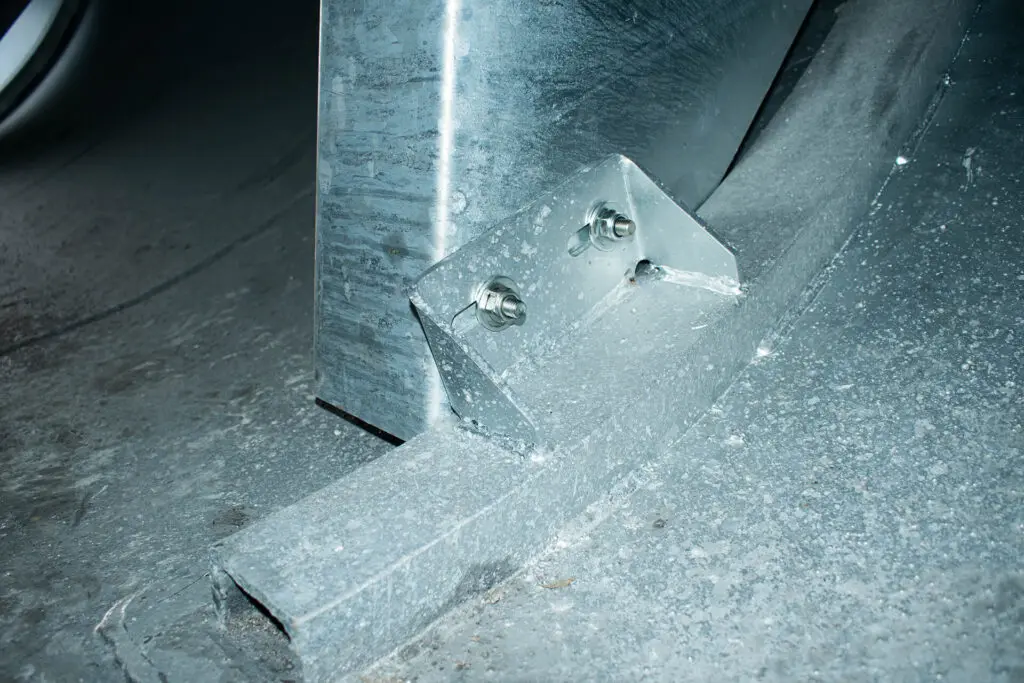
Manufacturing Processes
Equally as important as the materials and design is the manufacturing process and how it’s all put together. The manufacturing process should also aim to ensure structural integrity and long term durability.
Nevada slurry tankers go through a special manufacturing process where the reinforcing channels are submerged arc welded to the steel plates before the tank is rolled. This adds strength by creating a tank made from one piece so that there is no separation or areas where rust can form.
Galvanising is the only way to provide corrosion protection over the entire tank, including the joints. All Nevada tanks are hot-dip galvanised inside and out with the galvanising process being performed before the tank is put together. This ensures every crevice is protected from corrosion.
For the best corrosion protection, Nevada takes galvanising to the next level by adding a coat of clear lacquer to the outside which further protects the galvanising itself. This added layer not only adds to the lifespan of the tank but keeps it in good condition and makes it easier to clean.