Why do slurry tanker vacuum pumps need oil?
Vacuum pump oil does a whole lot more than just lubricate the pump. It’s needed for:
- Sealing – vacuum pump oil seals the pump so it can draw the air out.
- Cooling – the oil helps to keep the pump cool under pressure, reducing the wear and increasing the duty cycle.
- Corrosion protection – the oil works to flush out abrasive contaminants so they are not left to wear on the pump when sitting idle.
- Noise reduction – a smooth functioning pump is a whole lot quieter than one that’s struggling to perform!
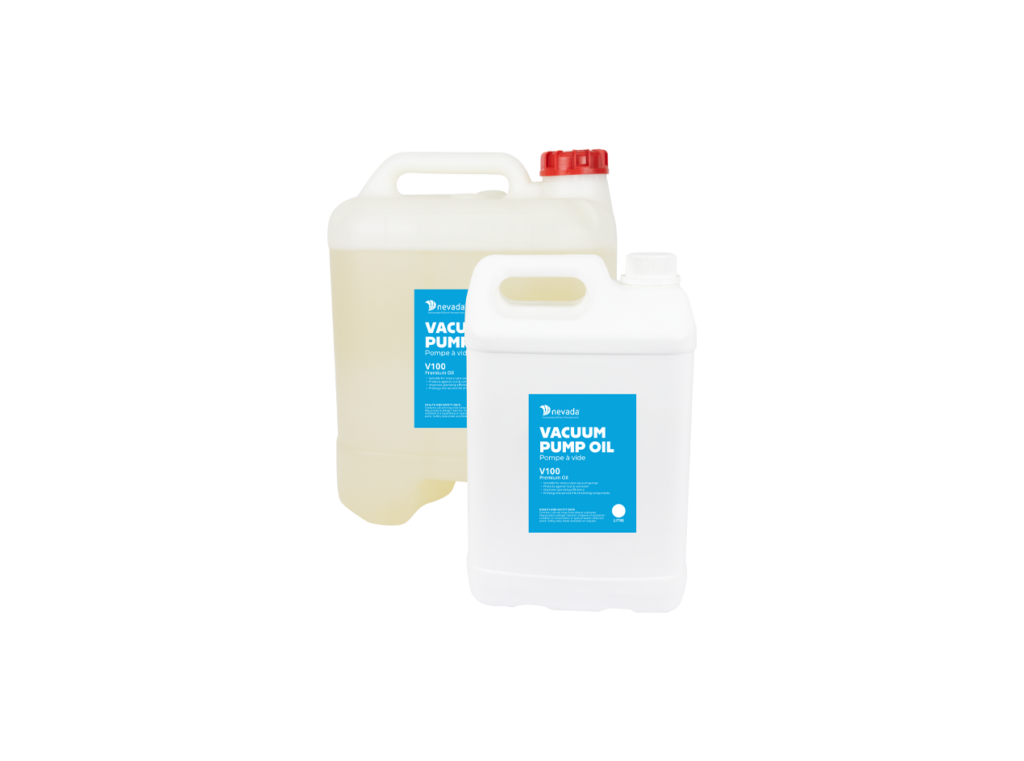
What happens if the vacuum pump is not correctly lubricated?
Feeding the vacuum pump too much or too little oil will affect the performance of the pump and reduce its lifespan. This is mainly due to:
- Excessive wear on the vanes from corrosive materials being pumped without enough lubrication.
- Overheating of the pump, reducing the duty cycle and causing damage.
- Corrosion of the pump from abrasive materials not being flushed out.
When does a slurry tanker vacuum pump need oil?
Slurry tanker vacuum pumps are auto-lubricating, meaning oil is automatically distributed every time the pump is running. Just like a car, the oil needs to be kept topped up, and it’s important to follow manufacturers recommendations on how much oil should be fed through.
Nevada slurry tanker vacuum pumps require 1 drop of vacuum pump oil every 1-2 seconds.
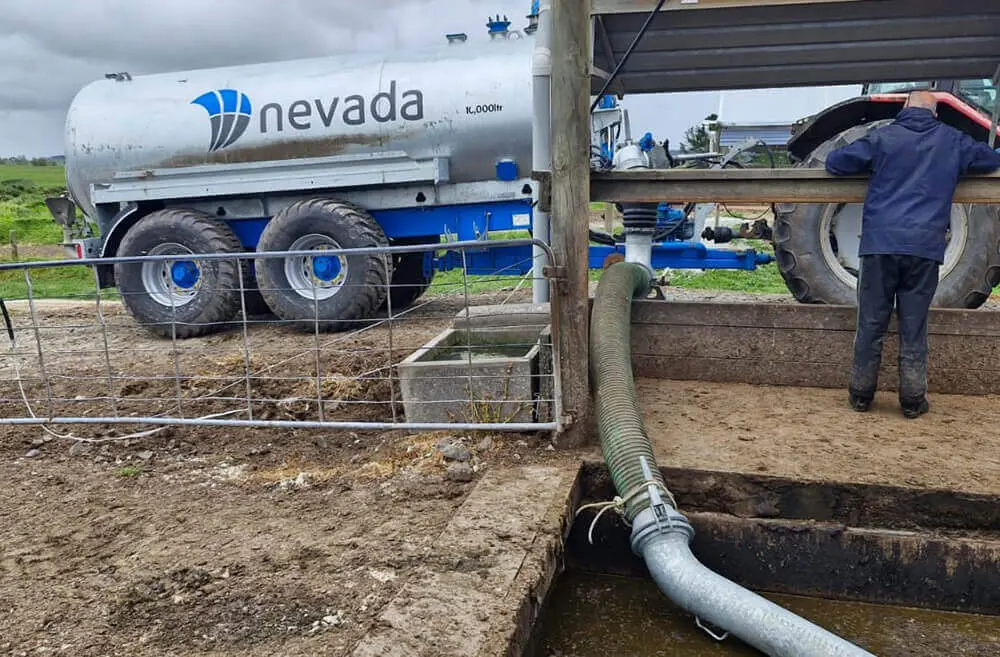
Why use Nevada Vacuum Pump Oil?
Nevada’s vacuum pump oil is fit for purpose and specially formulated to perform in the conditions your slurry tanker is working in. Here’s what you can expect from Nevada Vacuum Pump Oil:
- Excellent resistance to oxidative breakdown caused by exposure to air at high discharge temperatures
- Higher thermal stability for a reduction in carbon deposit formation
- This improves the vacuum pump’s operating efficiency.
- Reduces vane sticking and maintains the heat transfer efficiency.
- Low volatility reduces oil carry-over and wastage
- Improved viscosity index and good low temperature properties for all season operation
- Improved film thickness at high temperatures.
- Better cold temperature fluidity for low temperature start-up.
- Good protection against wear
- Prolongs the service life of working components like rotor bearings and vane tips.
- Protection against rust and corrosion